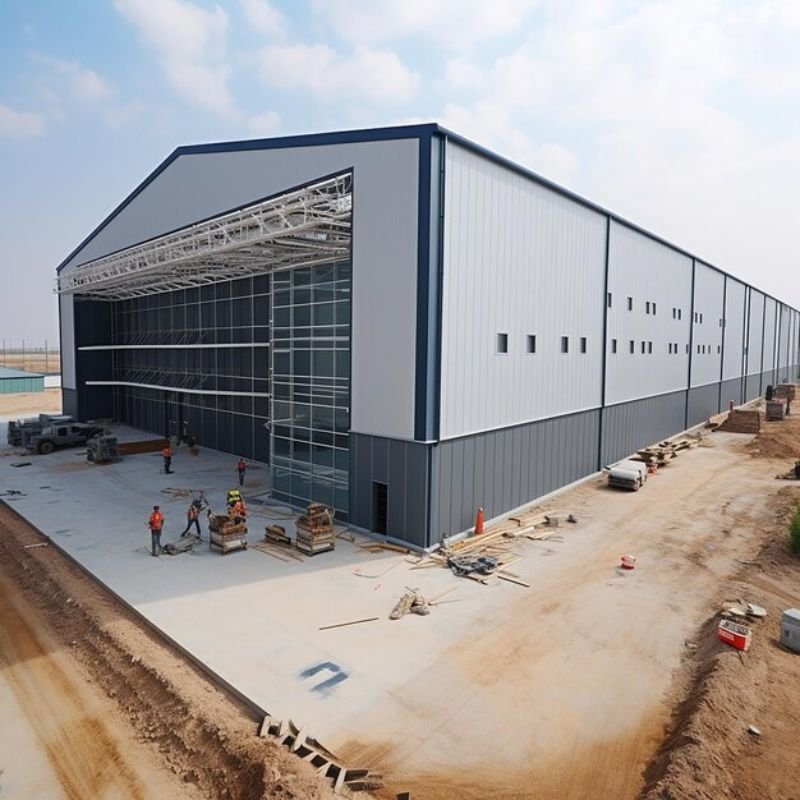
From Blueprint to Completion: ACCO’s Journey in Warehouse Design
From Blueprint to Completion: ACCO’s Journey in Warehouse Design
When it comes to constructing a warehouse, ACCO’s process from blueprint to completion is meticulously planned and executed to ensure that every client’s needs are met with precision and innovation. Their methodical approach, encompassing design, engineering, construction, and post-construction services, helps businesses stay on schedule, within budget, and ahead of their competition.
The journey is more than just about building a warehouse—it’s about crafting a space that improves operational efficiency, integrates cutting-edge technology, and anticipates future growth. Below is a detailed table outlining the key steps and features involved in ACCO’s journey from blueprint to warehouse completion.
Table: ACCO’s Warehouse Design Journey
Step | Description |
---|---|
1. Initial Consultation | ACCO begins with a comprehensive consultation, understanding the client’s requirements, such as storage needs, logistics, environmental factors, and future business expansion goals. |
2. Feasibility Study & Site Assessment | ACCO conducts feasibility studies and evaluates potential locations, assessing factors such as zoning, accessibility to transportation routes, and environmental impact assessments. |
3. Custom Warehouse Blueprint Design | ACCO’s expert design team creates customized blueprints tailored to the specific operational needs of the business, maximizing storage efficiency and workflow. |
4. Engineering & Technical Design | Engineering teams focus on structural integrity, climate control, load-bearing capacities, and material handling systems while integrating automation and energy-efficient technologies. |
5. Obtaining Permits and Compliance | ACCO handles all regulatory requirements, including securing building permits, adhering to local zoning laws, and ensuring the design complies with industry safety and environmental regulations. |
6. Material Selection | ACCO carefully selects high-quality materials, ensuring they are durable, fire-resistant, and energy-efficient, while incorporating sustainable building practices. |
7. Construction Planning | A detailed construction plan is developed, including timelines, budget tracking, procurement schedules, and assigning experienced project managers to oversee the entire process. |
8. Warehouse Construction | The physical construction begins, with ACCO’s skilled team managing everything from laying the foundation to installing advanced infrastructure, ensuring precision and structural integrity. |
9. Technology & Automation Installation | ACCO integrates automation systems, such as conveyor belts, robotics, and warehouse management systems (WMS), into the design to optimize operations and future-proof the facility. |
10. Quality Control & Safety Inspection | ACCO conducts rigorous quality checks and safety inspections, ensuring the building meets all structural, fire, and safety standards, and that the project adheres to timeline commitments. |
11. Client Handover & Training | ACCO offers a smooth handover of the completed facility, including training staff on using automation systems, managing workflows, and providing operational support for a seamless transition. |
12. Post-Completion Support | Even after completion, ACCO provides ongoing maintenance, support services, and flexible options for future upgrades or expansions based on the client’s growth and technological advancements. |
In-Depth Look: ACCO’s Warehouse Design Journey
1. Initial Consultation
The journey begins with a collaborative consultation where ACCO works closely with the client to understand their goals, challenges, and operational needs. Whether it’s storage capacity, distribution flow, or automation integration, ACCO focuses on designing solutions that cater to the specific business requirements.
Key Activities:
- In-depth needs analysis.
- Review of logistical challenges and operational inefficiencies.
- Discussion on long-term business growth and scalability.
2. Feasibility Study & Site Assessment
Once the needs are outlined, ACCO conducts feasibility studies, which assess whether the proposed design is practical for the location, and performs a site assessment to ensure the site is optimal for the warehouse’s design.
Key Activities:
- Zoning analysis.
- Environmental assessments.
- Evaluation of site access to major transportation routes.
3. Custom Warehouse Blueprint Design
Based on the client’s input and site assessment, ACCO’s design team creates a custom blueprint. The blueprint is carefully crafted to meet industry-specific requirements such as storage layout, automation capabilities, and climate control systems.
Key Elements:
- Space optimization with customized racking and storage solutions.
- Inclusion of loading docks and material handling systems.
- Advanced layout design for smooth workflow and productivity.
4. Engineering & Technical Design
ACCO’s engineering team brings the blueprint to life, working on the technical aspects of the structure, including load-bearing capacities, structural integrity, HVAC (Heating, Ventilation, and Air Conditioning), and automation technology integration.
Key Activities:
- Structural analysis to ensure the warehouse meets load requirements.
- Designing electrical, mechanical, and plumbing systems.
- Integration of energy-efficient systems like LED lighting and climate controls.
5. Obtaining Permits and Compliance
Navigating regulatory frameworks can be challenging, but ACCO manages all permit applications and ensures the design complies with local, state, and federal regulations, including industry-specific guidelines for safety and environmental impact.
Key Compliance Areas:
- Zoning laws.
- Safety regulations (e.g., OSHA compliance).
- Environmental standards for sustainability (e.g., LEED certification).
6. Material Selection
ACCO takes great care in selecting high-quality materials that not only meet the performance needs but also align with sustainability goals. Durable, fire-resistant, and weatherproof materials are chosen to ensure the warehouse’s longevity.
Material Features:
- Fire-resistant and weatherproof coatings.
- Sustainable building materials that reduce environmental impact.
- High load-bearing floors for machinery and heavy equipment.
7. Construction Planning
Before breaking ground, ACCO develops a comprehensive construction plan that outlines every phase of the project. This includes budget management, procurement, and assigning a project manager responsible for meeting deadlines and ensuring smooth execution.
Construction Plan Includes:
- Timelines and milestones.
- Budget allocation and tracking.
- Procurement of materials and subcontractor management.
8. Warehouse Construction
With a well-defined plan in place, construction begins. ACCO’s experienced teams handle everything from laying foundations to erecting steel frameworks, all while ensuring that every detail adheres to the highest standards of quality and safety.
Construction Activities:
- Foundation and structural work.
- Installation of HVAC, electrical, and plumbing systems.
- Setting up automation-ready infrastructure.
9. Technology & Automation Installation
To streamline warehouse operations, ACCO installs advanced technology, including automated material handling systems, robotics, and warehouse management systems (WMS). These systems are critical for improving efficiency and reducing operational costs.
Technology Integration:
- Conveyor systems for automated sorting and storage.
- Robotics for picking, packing, and palletizing.
- Integration with WMS for real-time inventory tracking and management.
10. Quality Control & Safety Inspection
Throughout the construction process, ACCO conducts continuous quality control checks. Once construction is completed, a final safety inspection is carried out to ensure the building meets all safety, fire, and structural standards.
Quality Assurance:
- Structural integrity inspections.
- Fire safety system checks (e.g., sprinkler systems).
- Ensuring compliance with all regulatory and safety standards.
11. Client Handover & Training
Upon project completion, ACCO provides a full handover, including all operational documentation, system guides, and in-depth training for staff. This ensures the client can seamlessly manage day-to-day operations and make the most of the new facility.
Handover Process:
- Training on warehouse management systems.
- Guidance on the use of automation and logistics systems.
- Documentation of safety protocols and maintenance schedules.
12. Post-Completion Support
ACCO doesn’t stop at project completion. They offer ongoing support, including maintenance services and options for future upgrades or expansions as the client’s business continues to grow.
Post-Completion Services:
- Maintenance and repair services.
- Future expansions and upgrades.
- Continuous operational support.
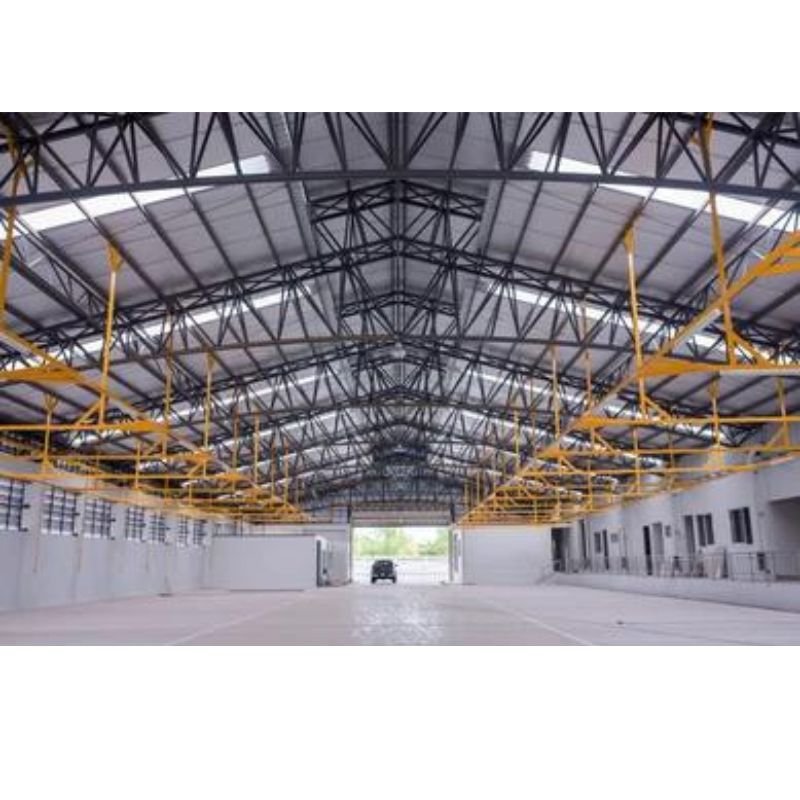