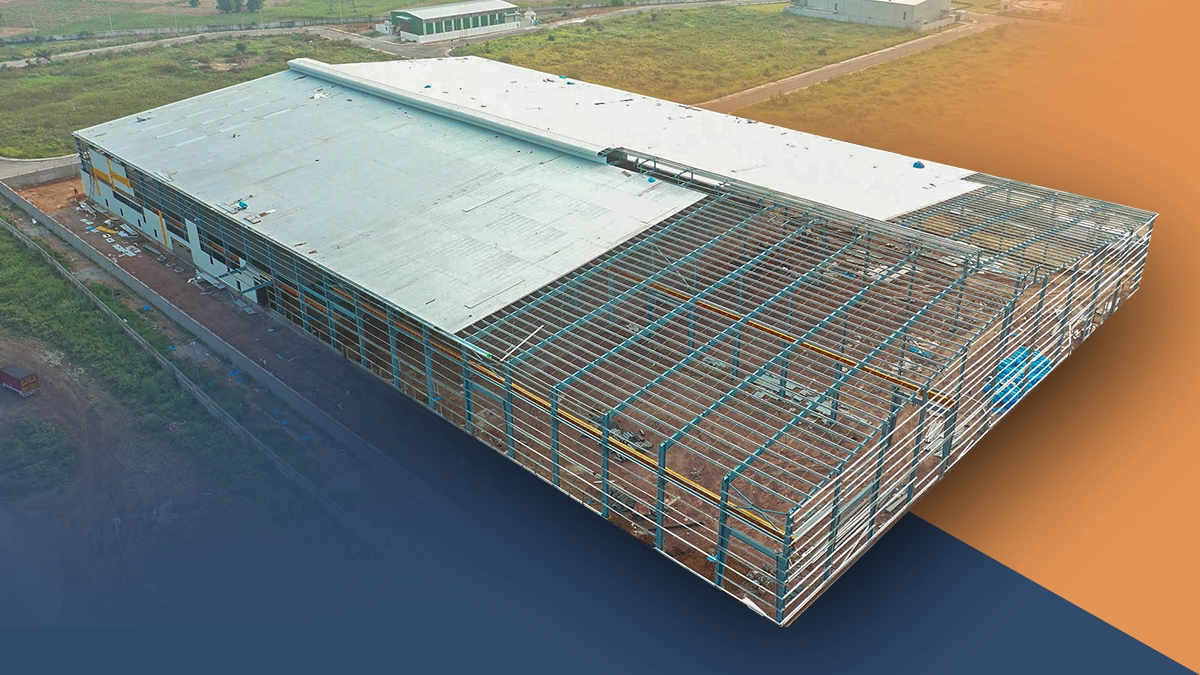
Pre-Engineered Buildings | Warehouse steel buildings
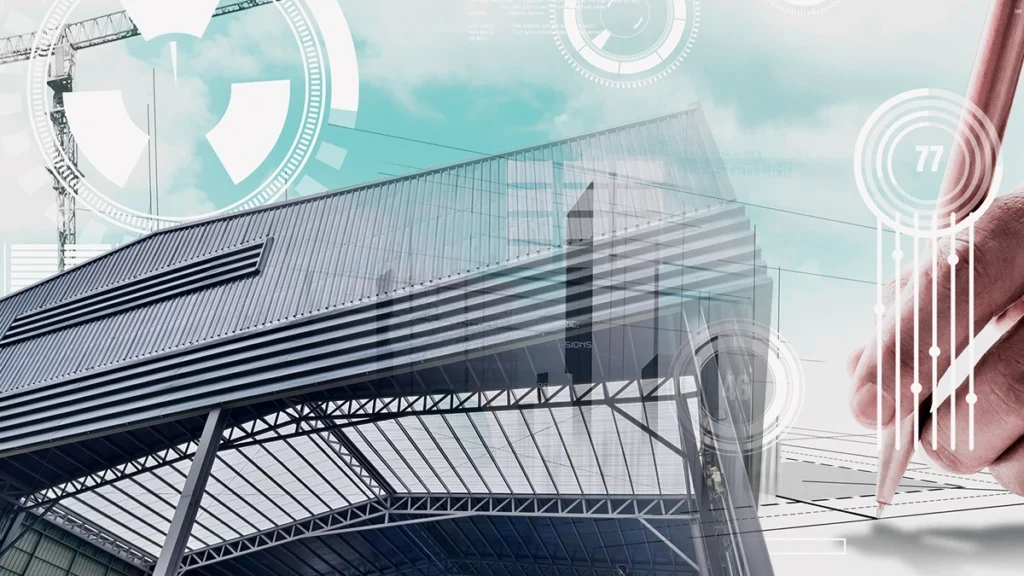
Pre-Engineered Buildings | Warehouse Steel Buildings
Outline of the Article:
-
Introduction
-
Overview of Pre-Engineered Buildings (PEBs)
-
Importance of Warehouse Steel Buildings
-
-
What Are Pre-Engineered Buildings (PEBs)?
-
Definition and Concept
-
Difference Between PEBs and Conventional Structures
-
-
Advantages of Pre-Engineered Buildings
-
Cost Efficiency
-
Faster Construction
-
High Durability and Strength
-
Eco-Friendly Solutions
-
-
Why Choose Steel for Warehouse Construction?
-
Strength and Load-Bearing Capacity
-
Low Maintenance
-
Fire and Weather Resistance
-
-
Applications of Pre-Engineered Buildings
-
Warehouses
-
Manufacturing Plants
-
Commercial and Industrial Use
-
Aviation and Agricultural Structures
-
-
Components of a Warehouse Steel Building
-
Primary Framing
-
Secondary Framing
-
Roof and Wall Panels
-
Insulation and Ventilation
-
-
Design Considerations for Warehouse Steel Buildings
-
Load-Bearing Capacity
-
Space Optimization
-
Energy Efficiency and Sustainability
-
-
How Pre-Engineered Buildings Reduce Construction Time
-
Pre-Fabrication Process
-
Quick Assembly and Installation
-
Lesser Workforce Requirement
-
-
Cost Analysis of Pre-Engineered Buildings
-
Initial Investment vs. Long-Term Savings
-
Comparison with Conventional Construction
-
-
Customization Options for Warehouse Steel Buildings
-
Size and Layout
-
Interior and Exterior Finishing
-
Additional Features (Mezzanine Floors, Loading Docks, etc.)
-
-
Sustainability of Pre-Engineered Buildings
-
Recyclability of Steel
-
Energy-Efficient Designs
-
Contribution to Green Building Certifications
-
-
Challenges in Constructing Pre-Engineered Warehouses
-
Design Limitations
-
Transportation and Logistics
-
Site Preparation
-
-
Future Trends in Pre-Engineered Buildings
-
Smart Warehouses
-
Integration of Renewable Energy Sources
-
Advanced Material Technology
-
-
Case Study: Successful Implementation of PEB Warehouses
-
Real-Life Examples
-
Benefits Realized
-
-
Conclusion
-
Summary of Key Takeaways
-
Why Businesses Should Invest in PEB Warehouses
-
Introduction
Pre-engineered buildings (PEBs) have revolutionized the construction industry by providing cost-effective and efficient solutions. Among the most common applications of PEBs are warehouse steel buildings, which offer durability, flexibility, and sustainability. This article explores the benefits, applications, and future trends of pre-engineered warehouse buildings.
What Are Pre-Engineered Buildings (PEBs)?
Pre-engineered buildings (PEBs) are steel structures manufactured off-site and assembled on location. Unlike traditional construction methods, which involve designing and fabricating each component separately, PEBs come with pre-designed components, making the construction process significantly faster and more efficient.
Difference Between PEBs and Conventional Structures
-
PEBs: Manufactured off-site, quick assembly, lower labor costs.
-
Conventional Buildings: Constructed on-site, longer construction period, higher costs.
Advantages of Pre-Engineered Buildings
Cost Efficiency
PEBs reduce material waste, labor costs, and construction time, making them a budget-friendly option.
Faster Construction
Since components are pre-manufactured, PEB warehouses can be erected in weeks rather than months.
High Durability and Strength
PEBs are designed to withstand harsh weather conditions, seismic activities, and heavy loads.
Eco-Friendly Solutions
With recyclable steel and energy-efficient designs, PEBs contribute to sustainable construction practices.
Why Choose Steel for Warehouse Construction?
Steel is preferred for warehouses due to its:
-
Strength: Supports heavy loads and equipment.
-
Low Maintenance: Resistant to pests, moisture, and corrosion.
-
Fire Resistance: Reduces fire hazards compared to wooden structures.
Customization Options for Warehouse Steel Buildings
Warehouse steel buildings can be customized based on:
-
Size & Layout: Adjusted according to business needs.
-
Finishing Options: Aesthetic enhancements, color choices.
-
Additional Features: Mezzanine floors, ventilation systems, loading docks.
Future Trends in Pre-Engineered Buildings
Smart Warehouses
Automation and AI integration are shaping the future of warehouse construction.
Integration of Renewable Energy Sources
Solar panels and energy-efficient lighting enhance sustainability.
Advanced Material Technology
New coatings and high-strength steel improve longevity and performance.
Conclusion
Pre-engineered warehouse steel buildings are an innovative solution for modern storage needs. They offer cost-efficiency, durability, and customization, making them an ideal choice for businesses looking for scalable infrastructure. Investing in a PEB warehouse can provide long-term benefits, making it a smart move for companies in various industries.
FAQs
-
Are pre-engineered buildings more affordable than traditional buildings?
Yes, PEBs are generally more cost-effective due to reduced material waste and faster construction times. -
How long does it take to construct a PEB warehouse?
Depending on the size, a PEB warehouse can be built within a few weeks. -
Can PEB warehouses be expanded in the future?
Yes, PEB structures offer flexibility for future expansion based on business needs. -
Are pre-engineered buildings energy-efficient?
Yes, PEBs can be designed with insulation, energy-efficient roofing, and ventilation systems. -
Do PEB warehouses require frequent maintenance?
No, steel structures require minimal maintenance compared to conventional buildings.
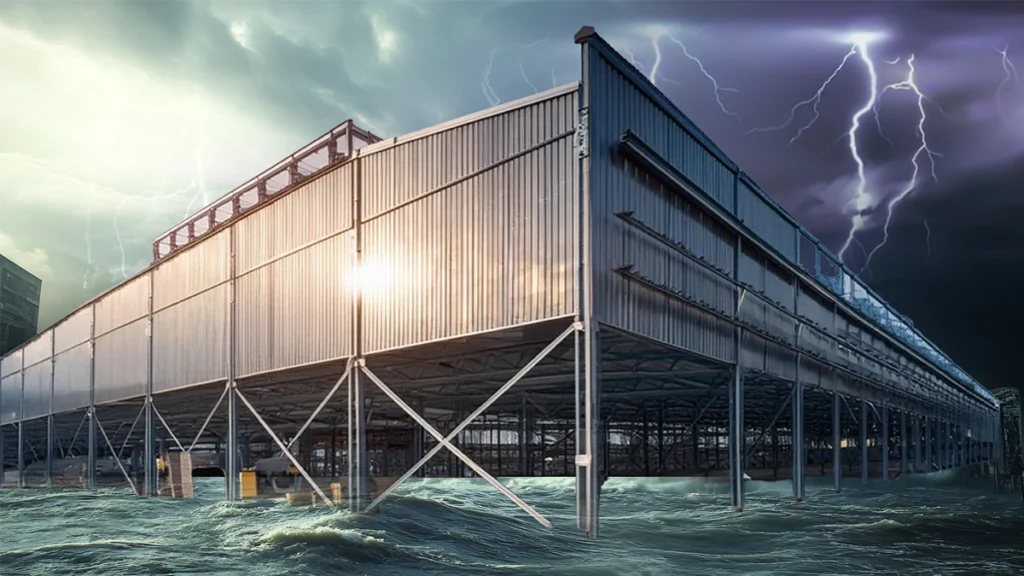
Pre-Engineered Buildings: The Future of Warehouse Steel Buildings
Introduction
In the realm of modern construction, Pre-Engineered Buildings (PEBs) have emerged as a revolutionary solution, particularly for warehouse steel buildings. These structures are designed and fabricated off-site, then assembled on location, offering a plethora of benefits over traditional construction methods. This article delves into the intricacies of PEBs, their advantages, applications, and why they are becoming the go-to choice for warehouse construction.
What Are Pre-Engineered Buildings?
Pre-Engineered Buildings (PEBs) are steel structures that are manufactured in a factory and then shipped to the construction site for assembly. These buildings are designed using sophisticated software that ensures precision and efficiency. The components are pre-cut, pre-drilled, and pre-welded, which significantly reduces construction time and labor costs.
Components of PEBs
-
Primary Framing: This includes the main structural elements such as columns and rafters.
-
Secondary Framing: Comprises purlins, girts, and eave struts that support the roof and wall panels.
-
Roof and Wall Panels: These are the outer layers that provide insulation and protection from the elements.
-
Accessories: Includes doors, windows, skylights, and ventilation systems.
Advantages of Pre-Engineered Buildings
1. Cost-Effectiveness
One of the most significant advantages of PEBs is their cost-effectiveness. The materials used are typically less expensive than those in traditional construction, and the reduced labor costs further contribute to overall savings.
2. Speed of Construction
Since the components are pre-fabricated, the assembly process is much faster. A warehouse steel building can be erected in a matter of weeks, compared to months for traditional construction.
3. Durability and Strength
Steel is known for its strength and durability. PEBs are designed to withstand harsh weather conditions, making them ideal for warehouses that need to store valuable goods.
4. Flexibility in Design
PEBs offer a high degree of flexibility in design. They can be customized to meet specific requirements, whether it’s for a small storage facility or a large industrial warehouse.
5. Sustainability
Steel is a recyclable material, making PEBs an environmentally friendly option. Additionally, the precision in manufacturing reduces waste, further enhancing their sustainability.
Applications of Pre-Engineered Buildings
1. Warehouses and Distribution Centers
PEBs are ideally suited for warehouses and distribution centers due to their large, open interiors that can be easily customized for storage needs.
2. Manufacturing Facilities
The strength and durability of PEBs make them perfect for manufacturing facilities that require robust structures to house heavy machinery.
3. Agricultural Buildings
From barns to storage sheds, PEBs offer a cost-effective and durable solution for agricultural needs.
4. Commercial Buildings
PEBs are also used in the construction of commercial buildings such as retail stores, showrooms, and offices.
5. Aircraft Hangars
The large, open spaces required for aircraft hangars are easily achievable with PEBs, making them a popular choice in the aviation industry.
The Engineering Behind PEBs
1. Design Process
The design process of PEBs involves the use of advanced software that allows for precise calculations and simulations. This ensures that the building will be structurally sound and meet all necessary codes and regulations.
2. Material Selection
High-quality steel is the primary material used in PEBs. The type of steel selected depends on the specific requirements of the building, such as load-bearing capacity and environmental conditions.
3. Fabrication
The fabrication process involves cutting, drilling, and welding the steel components according to the design specifications. This is done in a controlled factory environment, ensuring high quality and consistency.
4. Erection
Once the components are fabricated, they are shipped to the construction site for assembly. The erection process is quick and efficient, with cranes and other machinery used to position the components accurately.
Why Choose PEBs for Warehouse Construction?
1. Customization
PEBs can be tailored to meet the specific needs of a warehouse, whether it’s for storage, distribution, or manufacturing. The flexibility in design allows for the inclusion of features such as mezzanines, docks, and office spaces.
2. Scalability
As businesses grow, their storage needs often increase. PEBs can be easily expanded to accommodate additional space, making them a scalable solution for growing businesses.
3. Low Maintenance
Steel structures require minimal maintenance compared to traditional buildings. This reduces long-term costs and ensures that the building remains in good condition for years to come.
4. Energy Efficiency
PEBs can be designed with energy-efficient features such as insulated panels and natural lighting, reducing energy consumption and lowering utility costs.
5. Compliance with Regulations
PEBs are designed to meet all local building codes and regulations, ensuring that the warehouse is safe and compliant with all legal requirements.
Case Studies: Successful PEB Warehouse Projects
1. Amazon Distribution Center
Amazon has utilized PEBs for several of its distribution centers. The speed of construction and cost-effectiveness of PEBs have allowed Amazon to rapidly expand its logistics network.
2. Walmart Warehouse
Walmart has also adopted PEBs for its warehouses. The durability and flexibility of PEBs have enabled Walmart to efficiently manage its vast inventory.
3. Tesla Gigafactory
Tesla’s Gigafactory is another example of a successful PEB project. The large, open spaces required for manufacturing electric vehicles were easily achieved with PEBs.
Future Trends in PEBs
1. Integration of Smart Technology
The future of PEBs lies in the integration of smart technology. This includes the use of sensors and IoT devices to monitor the structural health of the building and optimize energy usage.
2. Advanced Materials
Research is ongoing into the development of advanced materials that can further enhance the strength and durability of PEBs. This includes the use of high-strength steel alloys and composite materials.
3. Sustainable Practices
As sustainability becomes a greater concern, the construction industry is moving towards more eco-friendly practices. PEBs are at the forefront of this trend, with a focus on reducing waste and using recyclable materials.
4. Modular Construction
Modular construction is an emerging trend that involves the use of pre-fabricated modules that can be quickly assembled on-site. This approach is closely related to PEBs and offers similar benefits in terms of speed and cost-effectiveness.
Conclusion
Pre-Engineered Buildings (PEBs) have revolutionized the construction industry, particularly in the realm of warehouse steel buildings. Their cost-effectiveness, speed of construction, durability, and flexibility make them an ideal choice for a wide range of applications. As technology continues to advance, the future of PEBs looks promising, with trends such as smart technology integration, advanced materials, and sustainable practices leading the way.
Whether you’re looking to build a new warehouse, expand an existing facility, or explore innovative construction methods, PEBs offer a solution that is both practical and forward-thinking. By choosing PEBs, you’re not just investing in a building; you’re investing in the future of construction.